Origins of Sheet Metal Fabrication
Metal working in one form or another can be traced back many centuries, with ancient jewellery cold formed from precious metals such as gold and silver. The discovery of melting metals expanded applications of metallurgy significantly and metals began to be used much more widely in the production of everyday items, particularly for military use. Metal would be heated and then hammered into flat sheets before being wrapped around wooden shields or applied to objects as armour.
The major breakthrough for sheet metal came around 1480 with the invention of the first metal rolling mill, which allowed for sheet gauge to be set using two cylindrical rollers with parallel axes to modify its thickness. Around the same time, cold machining of ductile materials was explored and by the 1600’s, machinery was capable of cutting and forming metal using animal or Hydraulic force, used for example, to form coins.
Fast forward to today and the basic principles of sheet metal fabrication have not changed. Different types of metals are rolled flat into sheets of varying thickness and used for many different purposes depending on the metal’s properties. Machinery is used to form, perforate, cut and join the sheet metal together in different sizes and shapes.
The technology used to perform these processes has obviously advanced significantly and machines are now faster, more accurate, more reliable and more efficient than ever before. It is also possible to automate and connect these machines in a way that allows for them to communicate. This is where sheet metal fabrication now begins to utilise not only technology, but other principles and practices to optimise its production.
Lean Manufacturing
Lean manufacturing is a methodology that focuses on minimizing waste within manufacturing systems while simultaneously maximizing productivity and uses principles such as Kaizen or continuous improvement. Waste is seen as any manufacturing process that a customer would not believe adds value and would not be willing to pay for.
There are seven main wastes identified by the lean manufacturing methodology:
- Unnecessary transportation
- Excess inventory
- Unnecessary motion of people, equipment or machinery
- Waiting, whether it is people waiting or idle equipment
- Over-production of a product
- Defects, which require effort and cost for corrections
- Over-processing or putting more time into a product than a customer needs, such as designs that require high-tech machinery for unnecessary features
Utilising the advanced technology now available within sheet metal fabrication, it is possible to design a “smart factory” reliant on automation, machine connectivity and MRP to address all of the above manufacturing wastes, creating a more optimised and cost-effective service to customers. One such example is Alpha’s large scale automated STOPA storage system which acts as a central hub, around which all manufacturing processes are linked.
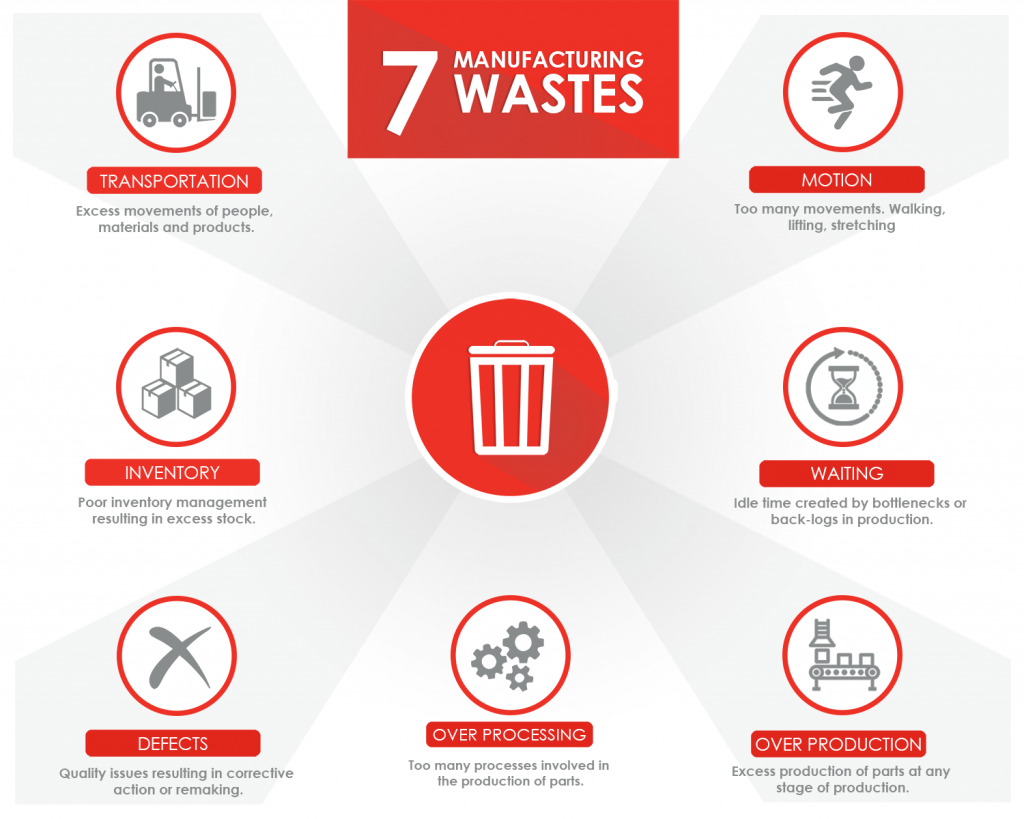
Factory Automation Example – STOPA Storage System
The STOPA storage system was installed as part of a strategic plan to create an optimised automated smart factory. It achieves this in 9 key areas:
- Optimized Flow of Materials
As the central hub for material storage, the STOPA is able to control and maintain a steady flow of raw materials, components and work-in-progress throughout the production process. In the background, data driven automated stock management informs key departments such as procurement, material planning, production planning and production management. This eliminates inefficiencies of siloed data or communication breakdowns and creates an integrated, optimised intra-logistical environment, resulting in increased productivity.
- Automated Chaotic Storage
Traditional manual storage of stock depends on pre-defined allocated spaces for different types of items, relying on manual records of each stock location to find required items. Chaotic storage allows any material to be stored in any available space within the STOPA system, almost at random. Intelligent stock management software automatically records the location of each part each time it is re-stocked, ready for the next time it’s called for. This removes the need for manual records of large inventories, eliminating potential errors which can slow down the manufacturing process as lost parts are searched for.
- Machine Integration
By integrating with the various machine softwares, the STOPA is able to communicate with each processing machine simultaneously. Delivering raw material and collecting processed parts from multiple machines continuously.
- Material Storage/ Production Interface
The STOPA system essentially acts as the central nervous system which connects material provisioning, material flow and processing. It automatically monitors and controls stock along this chain, creating an efficient end-to-end material flow. This improves efficiency in the manufacturing process and ultimately reduces production costs and lead times for the customer.
- Space saving
In total, the STOPA system runs 62 meters down the centre of the Alpha factory, with 230 pallet spaces stacked 12 high, allowing for storage of 600 tonnes of raw materials, components and work-in-progress over a relatively small footprint. By centralising this storage, space is freed up in other areas around the shopfloor, allowing for a more efficient and ergonomic factory layout.
- Safety
By dramatically reducing manual movements of raw material and parts around the factory, the potential for injury is decreased. Fewer forklifts are required for the transport of items between machines thanks to automated loading and unloading, while stock is added and removed from storage via automated delivery tables. Again, this removes the need for manual handling by an operator.
- Automated Machine Loading/ Unloading
Material is distributed to machines for processing as required by automated delivery tables before being placed on the machine bed by a mechanical lifting system. This reduces the time spent by an operator loading and unloading raw materials and parts, freeing them up for other value-added tasks. By removing manual handling from this process, risk of injury to operators I also significantly reduced.
- Avoidance of material damage
The lean manufacturing model is built on waste reduction and damage to material or parts can be a major source of waste within manufacturing. Items stored in the STOPA tower system are kept in a secure central place, away from any potential damage resulting in waste. By reducing manual movements of items and relying on the more accurate automated system, the potential for damage through human error is also minimised.
- ERP Integration
By integrating directly with ERP, the STOPA becomes central to manufacturing operations, assisting the flow of information between procurement, planning and production. Alpha Manufacturing use SAGE Enterprise for MRP (material requirement planning) which controls planning, inventory and scheduling, with the STOPA an integral part of this.
Salvagnini P4 Lean STOPA Integration Full 60m Length of the STOPA Storage System STOPA Integration into CNC Punch Machines
The Future of Sheet Metal Fabrication – Industry 4.0
Industry 4.0 is the biggest topic of discussion at the moment not only amongst manufacturing business leaders but also those involved in supply chain and logistics.
Industry 4.0 refers to the anticipated fourth industrial revolution as a result of technological advances in areas such as wireless, device inter-connectivity, robotics, machine learning and cloud storage. The integration of these technologies into what is described as a “cyber physical system” has the potential to ultra-streamline productivity, reduce costs and optimise logistics, thereby causing a revolution in global manufacturing.
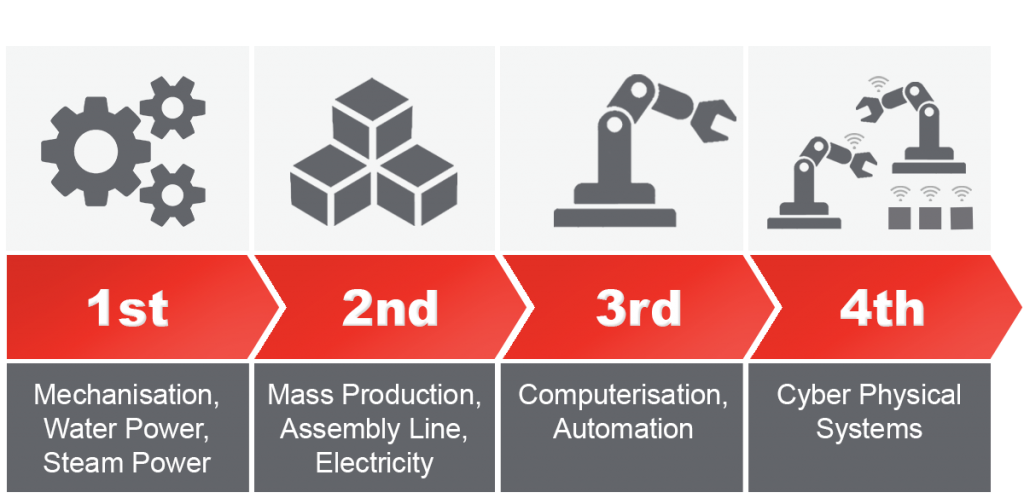
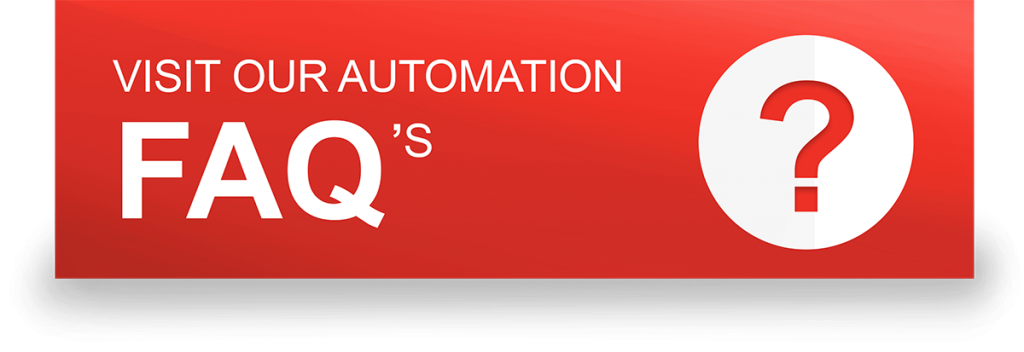